总工委员会
行业动态
连载丨大型钢管桁架空中拼装技术的应用研究(2)
来源:admin 浏览量:34 发布时间:2025-02-20 14:42:31
3.5 空中拼接
3.5.1 吊点的设置
用200 t汽车式起重机起吊,半榀主梁吊装时,采用4点绑扎起吊,吊点设在其三等分点附近的主弦杆和腹杆节点处,并设置手拉葫芦调节吊装角度。吊钩设于重心正上方位置。吊装前在桁架两端主弦杆上各绑扎1根直径15.5 mm的6×19 mm(公称抗拉强度1 550 MPa)中间芯为纤维芯的钢丝绳,作为吊装时的缆风绳对构件吊装进行方向控制,且在跨中上弦杆绑扎同规格2根缆风绳,待桁架落位后往两侧对拉45°与地面埋件进行连接。
3.5.2 起吊钢丝绳的验算
钢丝绳与构件长度之间的夹角取在45°~60°,按45°进行验算,安全考虑K值取10,选取钢丝绳承重量最大的工况进行典型计算。半榀主桁架最大吊重约18 t,采用4点绑扎,最不利吊装角度取45°(与水平面夹角),则单根最不利钢丝绳受力为63.6 kN。则绑扎点钢丝绳容许拉力为776.1 kN。
查钢丝绳选用表,绑扎点钢丝绳选用型号6X37S+FC(1770纤维芯),直径38 mm,采用4点吊装共用4根;该型号钢丝绳的破断拉力为843 kN>776.1 kN,满足要求。
3.5.3 桁架起吊时的自身工况验算
对吊装工况桁架作结构分析,对起吊的半榀主桁架内力分析时,按1.4倍(静荷载)的动力系数进行核算;变形分析按静荷载作用下的变形验算。
(1)用迈达斯分析软件验算,验算选用的桁架计算模型为单榀桁架的左部分(该半榀桁架杆件形式、跨度、质量具有代表性)。
验算结果表明,吊装时桁架外端位移最大为–5.66 mm,桁架挠度与跨度之比为1/2 853(小于规范要求的1/400;跨度为16.148 m);杆件最大应力比为0.13(小于规范要求的0.85),符合设计要求,可保证施工安全。
(2)拼接时的起重机站位:起重机站位位于每半品的中部位置,吊装半径20 m,起重机主臂使用44.9 m规格满足要求。如图5所示。
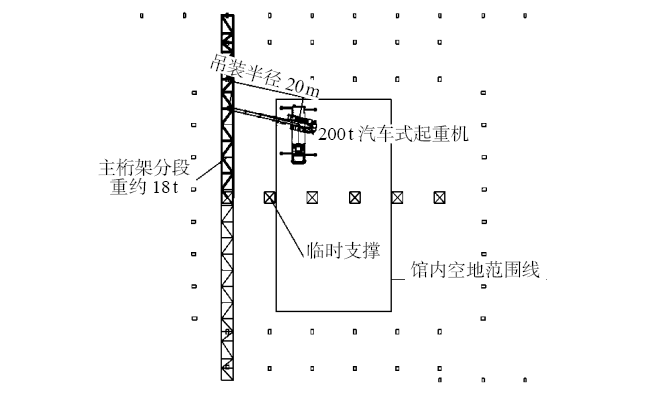
(a)
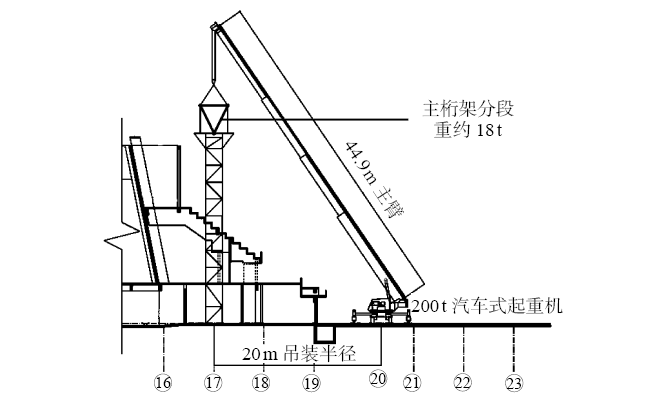
(b)
图5 起重机站位示意
(a)站位1;(b)站位2
3.5.4 起重机工况验算
最大吊重为18.0 t,起重机钢托座下设路基箱;为保证吊装过程中吊装力矩过大造成单侧土压应力过大,需验算该工况下的地基承载力,该工况下单个钢托座下部路基箱与地面接触面积为7.15 m2,最不利荷载取汽车式起重机自重的75 %+最大吊重,合计为634.5 kN。吊装过程分析:σ=ΣG/A=8.74 kPa<9.00 kPa。地基承载力满足施工要求。
3.5.5 吊装顺序及技术要点
先吊装拼装靠轴的第一榀、第二榀主桁架;再吊拼装靠轴的第六榀、第五榀主桁架;最后拼装中部的第三榀、第四榀主桁架。
为提高桁架的侧向刚度和便于铺设工作平台,在桁架上弦杆临时安装好檩条,便于人员操作,待主桁架及侧向桁架安装就位后再拆除。
安装前检查柱顶安装埋板和预埋螺栓的轴线位置和高程,合格后,将桁架的钢支座按设计要求临时安装在柱顶位置,钢支座在加工厂加工。
第一榀桁架安装时,拉好缆风绳固定同时吊钩一直不拆除,用另外一台200 t履带式起重机在外围进行侧向桁架的安装,保证主桁架的稳定性,主桁架中间拼装节点和支座节点焊接完毕检查合格后,拆除空中胎架的上端支撑点,下端支撑点继续承力。
随后轴的第二榀主桁架安装;第二榀主桁架对接拼装验收后,安第一榀、第二榀桁架间的侧向桁架,以保证第二榀桁架的稳定性。
轴处第六榀、第五榀桁架的安装也参照此顺序进行;最后安装的轴处第三榀、轴第四榀主桁架也按此要求执行。
在空中对接上下弦管时,钢管接口处设内衬管,对接管端部焊接耳板,作为对接时引导固定措施,接口焊接合格后,割除耳板。
3.6 拼接时的测量控制技术
3.6.1 地面胎架的组装测量控制
胎架的定位控制是桁架组装成型质量的关键技术工序,从以下两个方面进行控制。
(1)地面路基箱板的铺设:在整平的碎石土面按尺寸铺平铺实路基箱,平整度及高差超过20 mm时,应及时调整到位。
(2)地面胎架的测量控制:胎架组拼前,对地胎架的高度、宽度、长度、垂直度等进行测量校正,对节点杆件的搁置位置测设控制网,对杆件的空间位置进行测量放线,设置好杆件放置的限位托撑。胎架设置好斜撑,不得晃动。
为防止胎架底部的刚性平台板沉降引起胎架变形,设立沉降观测点。在组装中当荷载作用于下部路基板上时观察沉降变形状态,如有变化应及时采取校正措施,无变形时方能施焊。
3.6.2 桁架组拼测量控制
(1)组拼过程中的测量控制:桁架拼装过程中需对每一根弦杆、腹杆逐根进行测量放线,节点附近的支托点定位要二次复测。先就位弦杆,后组装腹杆,腹杆要从中间向两端进行组装;腹杆组装时须精对控制中心线,相贯线接口不能随意切割修正。特别对桁架的空中接口部位的精确控制,是保证空中完好对接的基础。
(2)组装完成后的测量控制:每半榀拼装完成后,用全站仪复测成型桁架节点的位置,确保与设计状态相符。
3.6.3 空中对接时测量控制
(1)根据设计的临时支撑架的地面位置,将中心线投测在地面基础的路基箱面上作为控制依据安装竖向临时支撑架,支撑架的顶标高按设计的标高用水准仪器和钢尺控制,顶部的中心位置和垂直度用全站仪控制,顶部的U形胎架在地面平台加工好,吊上去安装,并复测校正到位。
(2)空中的上下弦杆对中时,利用反射贴片进行坐标定位。
(3)对接时的温度要求:根据设计要求,空中合拢温度为15~25℃,因此合拢时宜安排在上午进行,使用全站仪测量时,温度稳定,误差较小。
3.7 对接部位的精度保证措施
为保证主管的顺利对接,在地面组合拼装时,在对接管口位置用定型模具控制变形,保证几何尺寸。空中对接时利用焊接耳板调整管口对接精度。
4 钢管桁架的空中卸载技术控制
4.1 卸载控制要求
主桁架空中对接采用临时撑架支撑,待结构形成稳定体系后再进行同步卸载。在空中拼装阶段,通过空中胎架支托将结构重力传至支撑架顶,支托底部预设钢垫板,卸载阶段,将千斤顶置入预留空间顶起底部主支托实施卸载。
(1)主桁架应力不超标,下挠值在设计验算范围内。
(2)卸载过程应同步平稳,以确保主桁架均衡、缓慢过渡到设计受力状态。
(3)支撑架在卸载过程中自身应力不超标。
(4)对卸载全过程进行实时监控。
(5)桁架所受荷载转化过程中,遵循“卸载同步、分级卸载、变形协调”的原则,通过释放分层垫板的高度,从而实现支撑架与主桁架的分离;通过分级同步卸载,微量下降来实现“荷载分步转移,杆件内应力重新分布”的状态。
4.2 卸载的分级
支托点分为4级同步卸载,每级卸载每个支托点采用2台千斤顶同步卸载;六榀主桁架同步卸载;卸载值及每级卸载时抽出的对应垫块厚度见表3。千斤顶型号QL10,千斤顶外形初始高度不大于280 mm。各支托点的反力见表4。
表4 各支托点的反力

4.3 卸载流程
卸载时需在桁架下弦杆与千斤顶之间设置防护板保护;卸载时同步顶起杆件约2 mm,移出第一块垫板,随后千斤顶同步回缩使桁架再次落至垫块上,检查卸载状况,无异常后继续下一次卸载。
第一步:布置千斤顶,略微顶起。
第二步:千斤顶锁紧后,抽出第1块卸载垫板,6个支托点同步抽出第一块垫板。
第三步:千斤顶缓慢回落;上部结构落至垫板上,检查卸载情况并确认无误。
第四步:排查桁架的变形情况,变形正常及焊缝质量无变化后,按同样步骤再次顶起上部结构,然后抽出垫板,再收缩回落,直至完成。
4.4 卸载控制措施
(1)卸载前对整个屋盖钢桁架结构变形、焊缝进行质量再复核检查。
(2)每个卸载点用钢板刻度尺对卸载量进行测量,对卸载点的实际卸载量进行记录。
(3)在主桁架和其他次桁架的跨中、1/4跨处的上、下弦杆位置及外端点设置变形监测点;每卸载一步,监测一次数据。当监测结果与模拟分析对比出现异常时,应及时通知负责人并立即停止卸载,组织相关专家分析原因,问题解决后,继续下一步卸载。
(4)待所有支托点全部完成卸载、桁架与支托点分离后,进行全部检查,检查跨中、跨四等分点处的扰度和变形,检查焊缝变化情况,检查支座的变形情况,与理论计算基本吻合时,方可拆除支撑架。
5 吊装过程中的纠偏措施
5.1 起吊阶段
半榀主桁架地面组装验收合格后,绑扎起吊;起吊离地约10 cm停止起吊,静置约30 min,检查倒三角桁架的竖向垂直情况,若大于5 mm要通过手拉葫芦纠正。
检查杆件的变形情况,测量端部变形是否与计算一致,若超出计算值,需采取应对措施后方可继续起吊;起吊过程要平稳,利用缆风绳辅助。
5.2 空中对接阶段
主桁架吊至安装位置时,下落要慢,距离支座约10 cm时停止下落,利用缆风绳和手拉葫芦精确对准柱顶及中间对接平台的轴线和控制线,平稳下落并精准对中。
后吊的半榀桁架在主管就位时,要反复多次调整才能精确就位。
5.3 整体卸载阶段
(1)每一榀主桁架拼装完后,复测核实支撑架下部支座的竖向变形数据,若有变化及时纠正,用楔形钢板及时顶紧。
(2)整体同步卸载时,用钢带尺复测各点卸载高度,误差不超过1 mm。
6 施工效果
篮球馆主跨管桁架采用空中拼装技术,解决了拼装场地不足的问题,能保证安全、节约工程费用、保障施工进度。
采用工厂下料、工地现场分段组装、空中拼装方法,施工质量有保证,经后期的屋盖结构荷载加载后,检测扰度数值情况,均满足设计要求。
7 结束语
通过管桁架空中对接施工技术在监利文体中心篮球馆屋盖管桁架结构施工应用研究表明,此对接技术对大跨度篮球馆、跨外吊装条件受限的情况,应用较为实用,效果较好。
(本文已完结)
摘自《建筑技术》2023年12月,张大禄