行业动态
大型机场通风空调系统DfMA设计及施工技术
来源:admin 浏览量:109 发布时间:2024-08-14 14:27:04
目前,我国大型复杂工程建设规模不断增加,面临的机电管线系统建设压力也越来越庞大复杂,传统的机电加工和安装模式严重制约着项目建设和行业发展,传统建筑模式也面临着劳动力短缺、人工成本上涨、环境污染、资源浪费等日益突出的问题。
机电安装工程作为工程项目中重要环节之一,涉及给排水、强弱电、消防、通风空调多个专业,多专业、多工序相互交叉造成施工质量控制和管理协调困难,因此要选择一种更高效高质便于管理的新方法,即DfMA(Design for Manufacturing and Assembly)模块化安装。DfMA模块化安装是指机电管线按照模块化设计并在工厂中生产加工成型、模块化组装完后,运至工地现场,通过可靠的连接方式快速安装。此方法可有效解决工期紧、人工费用高、现场环保等相关问题。
1 项目概况
某国际机场占地面积1 255万㎡,第三条跑道航站楼、停机坪等配套设施合同总造价136.94亿元。
T2C客运大楼分为西指廊区域、核心区域、北指廊区域以及南指廊区域,总建筑面积约30万㎡。设有面积约为1 500 ㎡的大型制冷机房2间,空调机房38间、风机房11间以及排烟机房10间。
其中制冷机房内冷冻水管为 1 600 mm大口径管道,且现场空间有限,如果按照常规方法进行施工,难度较大。行李区域为高跨度空间,风管采用常规方法安装尤为困难。经过多番讨论,决定将部分区域改为DfMA模块化安装,以提质增效,提高安全性及环保等级。
2 项目实施
以具有代表性的制冷机房及行李区域通风空调系统安装为例。实施流程如图1所示。
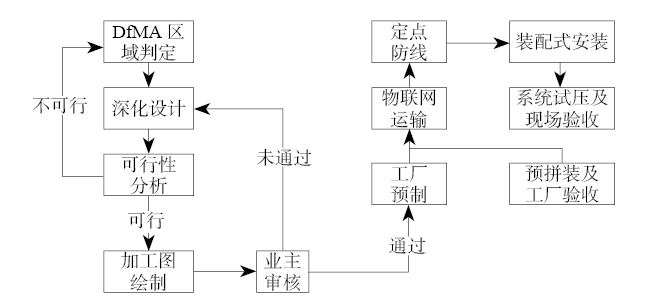
图1 实施流程
2.1 通风空调DfMA模块化施工区域识别
通风空调系统适合做DfMA模块化安装范围见表1。
表1 通风空调系统适合做DfMA模块化安装范围
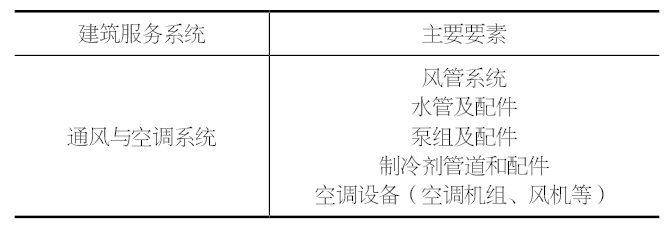
区域识别主要考虑因素主要有以下几方面。(1)管线数量因素。根据下发初版模型进行区域选择,管道成排直线段排布区域以及管线分层清晰区域。(2)区域属性因素。根据建筑结构墙体分布尽量选择空间开阔、路线平坦的区域,考虑上下楼层之间的结构运输洞口及场外进入上下楼层间运输通道是否满足模块运输要求;对于机房内部,要充足考虑设备及管道排布,合理规划管线模块运输路线与设备模块运输路线,以及机房门口是否有足够空间进行运输,并根据区域特点设计出运输规划图。(3)安装空间因素。选择模块区域时还需根据安装空间综合考虑,如机房区域是否足够行走顶升车及叉车等托举运输工具、模块顶升到达指定位置后两侧是否有足够空间上人进行固定及管道连接。综合以上因素将所选区域生成DfMA模块分布图。
2.2 制冷机房深化设计
2.2.1 图纸准备
由于本项目为正向设计,下发图纸中仅为意向设计方案,承包商需要根据要求进行负荷计算。对每处通风系统服务区域进行计算验证图纸合理性,之后将每个系统计算后提交ICE(Independent checking Engineer)审批,如有问题需重新计算并更改管线尺寸及设备选型再做提交,直至通过审批。具体步骤如下。(1)根据空调系统原理图查看对应系统中阀门及相关构件。(2)根据承包商DfMA设计后管道路由绘制出包含弯头、三通、变径、消音器以及阀门等构件位置的等距图,并对整个系统进行计算。(3)根据《风管配件摩擦系数参考表》计算出系统中每个配件的静压损失。(4)根据每个配件的静压损失反推,计算出风机或空调机组等设备所需静压。(5)根据最终确定静压选择相应的设备,从而通过ICE审批。
同样,对于空调水系统的计算,也需要根据系统长度及整体路径计算所需水泵的扬程及功率选择相应参数的设备,保证在水管末端能够有足够的流速,以及根据冷气系统服务区域计算出所需冷量,并匹配相应规格的冷机,保证整个制冷系统的使用功能满足要求。
2.2.2 管线排布原则
在图纸经过ICE审核后,承包商需根据最新的图纸更新机电模型,并链接建筑结构等相关专业模型,依据管线综合排布原则进行优化模型。
2.2.3 空间预留原则
(1)在通风管道模块区域排布时,需充分考虑模块安装过程中模块与模块之间、模块与非模块之间是否有足够的空间进行操作,以及模块与顶板之间的连接、模块与底板之间的固定等是否有足够空间。
(2)在制冷机房内,需考虑模块化安装区域的设备排布,需对机房内设备排布进行优化,以保证房间内可预留出合理的模块运输及维护检修通道,并生成检修口、检修通道分布图。同时,还要根据机房内竖向模块,综合考虑留出合理竖向运输空间以及检修空间。
2.2.4 阀门安装原则
通风与空调系统模块化设计时,需与墙体避开合理空间,保证模块安装与穿墙位置连接时能有足够阀门安装及检修空间。机房内模块区域的阀门应在模块安装后设置,安装在易于维护及检修操作的区域。运输过程中应将易损坏阀部件预留出空间,并将该阀部件运输到现场后进行安装。
2.3 空调水管及排烟风管模块切分
公共区域的成排风管及水管的模块划分需根据检修空间及吊顶吊杆位置进行合理切分,保证模块框架吊点能够避开吊顶吊杆位置。机房内模块的切分需根据维护及检修通道布置图进行成模数切分,并在切分完成后根据施工顺序绘制加工、安装工序图,以约束模块的加工及安装顺序。
2.4 安装方案复核
模块根据要求切分完成后,需对模块的场外运输及场内运输进行模拟分析。通过BIM软件按照选定运输路线进行模拟,检查是否可行 。对完成建筑结构尺寸进行实地扫描,记录扫描得到的点云数据。将扫描得到的点云数据进行逆向建模处理,得到可导入建模软件的建筑结构的实地模型与原有建筑结构模型进行对比,保证模型与现场一致,且保证能够准确定位及安装,如发现偏差较大且已影响到模块运输或安装,应立即调整方案及制订相关整改措施。
2.5 模块设计及加工图绘制
进行模块设计时需结合建筑、结构、精装等排布情况综合考虑,根据模块安装区域对模块吊装及连接进行设计,如空间狭小走廊区域,可制订两种吊挂安装方案。
(1)G形吊钩固定方案。为避免空间不足、无法在模块托举时进行顶部生根固定,可在模块安装前先按照模块分布图中吊杆布置详图将设计好的吊杆固定于顶板上,预留出G形挂钩,作为模块吊挂点。同时G形挂钩上需预留可调节螺栓孔,以便在模块存在偏差时进行纠偏处理。
(2)U形吊卡固定。同样需要将吊杆在模块安装前按照模块分布图中的吊杆布置详图固定于结构上,然后按照图纸将模块顶升至吊点位置,与预留吊杆进行连接固定。
在模块框架设计时,需严格按照管线最大负荷对框架进行负载计算,保证框架能够在机电系统正常运行情况下有足够的承载力,且要保证框架拼接处能有足够的强度。本项目所有结构框架设计均需通过结构工程师计算并签字确认后,才可进行加工生产等后续工作。
模块及框架设计完成后应根据要求进行绘制模块详图,其中包括但不限于以下内容。(1)整体模块尺寸及带有详图索引的模块三维轴测图。(2)根据模块管线层数,绘制标有详细管道系统及管线间距的各层管线平面图及剖面图。(3)模块框架三维轴侧图并带有框架内连接节点详图索引及重要构件编号。(4)根据各专业技术规范将管道固定方式、连接方式以及模块吊挂方式等详细地体现于模块详图中,并标注明确固定所需构件名称及选型,以便于模块进行精准装配。(5)包含以上所有构件及管道详细信息的配材料明细表,以便于对模块的运输及吊装设备进行选择。
2.6 加工生产
工厂需根据模块详图及加工、安装工序图进行模块内管线和框架的生产及拼装,并在加工完成后根据各专业规范要求进行模块的拼装工作。模块拼装完成后,需按顺序将模块在工厂进行预拼装并通过验收,以保证模块运输至现场后能够准确连接。
在模块运输之前,需先按照模块位置将带有模块基本信息(包括但不限于模块编号、安装位置、三维图纸、模块大小及重量、管道连接大样等信息)的二维码粘贴在模块统一位置,并在模块装车前用移动设备扫码录入物流信息,以便于管理人员实时查看物流信息。模块运输到现场后存储于模块堆放区,管理人员可在移动设备上实时查看模块数量、编号、存储位置等信息。
当模块开始安装后,可根据模块上二维码定位至模块在施工现场应安装位置,并显示运输路线图等信息。
2.7 运输及安装
2.7.1 场外运输
模块及管段从加工厂运输至现场前需将模块做好成品保护,防止运输过程中对模块造成损坏,影响后期安装。模块运输需根据现场安装计划、天气等原因有序排出单次运输模块数量及运输周期,列出详细运输计划,以保证现场模块安装进度。
2.7.2 场内运输
模块及管段运输到现场后根据场内运输规划图将模块按照不同尺寸选择相应运输路线,运输至安装位置附近的临时模块堆放区等待安装。
2.7.3 模块安装
对于机房区域。在装配式管道制作期间,按照CBWD图中设备基础图进行精准设备基础浇筑。并要在浇筑完成后进行复测,保证与模型的位置精准重合,同样隔震台座及弹簧减震器均需进行参数复核,保证与模型精准匹配。在模块安装之前应先按照机房深化设计图纸将部分落地大型支架安装到位。
(1)根据机房内运输规划图,将模块及管段运输至指定位置,并将运输通道边缘设置好安全警示线,无关人员不能进入运输区域。
(2)在预留好的结构吊钩上悬挂单轨吊车(吊装工具,根据不同尺寸模组选择对应吊装能力的设备)等待模块就位。
(3)使用叉车将部分小模块及管道运输至安装区域,较大管段(如 1 600 mm冷冻水管道管段)采用地坦克托运至指定位置。
(4)将管道模组在地面通过螺栓将Ω管箍、管座、弹簧支座及横担连接牢固,并保证连接后管段不超过3 600 mm,以满足吊装最大要求。
(5)使用两条可承重6 t的吊装带(根据不同尺寸的模组选择对应承载力的吊装带)系在管段上,使吊装带在管段上能够平衡受力。
(6)所有人员撤离至吊装区域3 m以外安全区,并需安全人员在场,启动单轨吊车,当管段离地300 mm时停止提升,静待30 s后确保吊运设备及管段稳固方可继续提升,直至吊运至指定位置。
(7)安装人员使用升降车到达指定高度,将模组段固定在已设置好的刚性支架上。
(8)重复此动作将余下预制管段吊装至指定位置,若已安装好的管道模组和被吊起的管道模组之间水平距离在50~100 mm,可使用丝杆水平横穿两组管道模组,以保证模组之间能够可靠连接。如果在100 mm以外,则需水平移动管段至已安装好的模组处,并用螺栓牢固连接及管道固定。
(9)利用扭力扳手,对每组螺栓进行扭矩测试,待完成扭矩测试,确保安装好的两段模组已牢固安装在永久性支架上后,方可将吊装工具慢慢释放高度,直到可以取下吊装带。
(10)重复2~9部操作,直到所有落地安装管道模组全部安装完成。
2.7.4 机房内顶板生根吊装管道模组安装
(1)使用放样机器人将支架吊点进行放线定位,利用升降车将吊架立柱提升至指定位置,并进行固定。(2)根据运输规划图,将模组运输至指定位置,在地面进行螺栓连接,且长度不宜超过1 200 mm。(3)在地面将管道Ω管箍、管座、减震支座及管道横担固定在拼装好的模组上。(4)将吊装带(满足管道负载)固定在特定托举工具上。(5)所有人员撤离至安全区域。(6)缓慢提升模组段直到距离地面300 mm,静待30 s后,确保调运设备及管段稳固方可继续提升,直至吊运至指定位置。(7)安装人员使用升降车到达指定高度,将横担固定于已安装完的立柱上,保证牢固连接。(8)利用扭力扳手,对每组螺栓进行扭矩测试,待完成扭矩测试、确保安装好的两段模组已牢固安装在永久性支架上后,方可将吊装工具慢慢释放高度,直到可以取下吊装带。(9)重复2~8部操作直到所有吊装管道模组全部安装完成。
2.7.5 设备安装定位
由于机房左边为室外行车道,可预留出足够大的设备运输空间,通过使用叉车、单轨吊车及地坦克相配合,将制冷机组运输至对应位置进行安装。
设备就位后将主管道与设备间嵌补段进行现场安装,以保证主管道与设备能够可靠连接。
2.7.6 行李区域通风空调模组安装
在模块安装前先按照模块分布图中吊杆布置详图,将带有G形吊钩的模块吊杆进行固定。
(1)按照运输规划图将运输通道边缘设置好安全警示线,保证无关人员不能进入运输区域。(2)使用模块运输车及特定胎架将模块按顺序运输至指定堆放区,运输过程中需安全人员全程在场监督。(3)利用放样机器人根据模块安装位置进行防线定位。(4)使用叉车将模块放置于可移动顶升车上,并加以固定。(5)模块运输至指定位置,在工作区域设置好安全警示线,顶升车操作员通过操作手柄控制顶升车升高至指定位置。(6)同时连接工作人员通过另外2台顶升车升至相应高度,将模块悬挂于已固定好的G形吊钩上,然后通过可调节螺栓孔及通丝吊杆调整模块位置,直到模块调整至合适位置。(7)将第二个模块以相同的方式提升至指定高度,工作人员将2个模块进行螺栓连接。(8)如连接过程中存在误差,应通过可调节吊杆消除误差,保证模块间可靠连接。(9)重复(2)~(8)的操作,直到所有模块安装完成。
3 结束语
针对机电管线传统安装中劳动力短缺、人工成本高、环境污染严重、资源浪费等问题,引进DfMA方法,并探讨了在面向制造和装配的设计上降本提质的作法,从而在根本上解决管道大、跨度高、危险性高、安装困难,以及在多标段、多专业移交地块时间不充足的问题,可大幅提高劳动生产率,减少环境污染。该技术在建筑领域具有广阔的发展空间,得到了同行业的认可。
摘自《建筑技术》2023年6月,张立超, 张 正, 冯智伟, 周 宁, 范 杰